How we collaborate on our EOW checklist
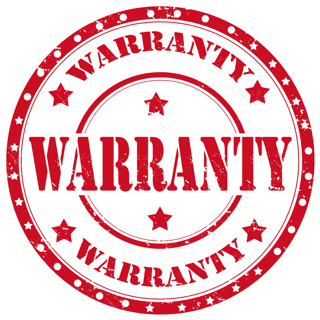
Throughout an assets lifetime there are certain milestones that occur for all owners. End Of Warranty is one of these milestones. Each owner want to have a checklist as complete as possible when doing and EOW inspection. Having a Platform with more than 30 energy companies on-board gives us the possibility to commonly build these checklists.
In this update we will share a sample of the first draft of our End Of Warranty Checklist so that you get a good idea for what it is we are developing. To have the sample please complete this form:
For obvious reasons we cannot share the common list being being developed at O2O WIND. Please note that the material is provided “as is”, and O2O WIND International assumes no responsibility whatsoever for it use or correctness.
Please fill in the form in the pop-up appearing at this page to have this first draft. Thereafter your update continues as it is.
How do EOW inspections tie in with the legal frameworks on the project?
Along with a standard supply agreement for the components, a warranty is provided. The length of these warranties may differ depending on the component, or even the market.
For example, it is a norm with the Wind Turbines to have standard 2 year warranty on the components. However, with the transformers this warranty can be a short as one year.
In most cases the warranty period is referred to directly as a warranty period under a specific clause within the agreement, while in some legal jurisdictions this is referred to as the Defects Liability Period or even the Defects Notifications Period.
In all of these, the basic premise is the same: there is a defined period to which the OEM has signed up, and if the part has not performed as designed or if it has failed, the OEM will replace that component without cost for the owner.
Different warranty types from the OEM
- Parts only Warranty, new parts are shipped to the project, however installation costs such as labour, cranes or downtime are excluded.
- Full Warranty – inclusive of installation costs
- Partial Warranty – excluding certain parts or a mix of a Parts warranty & Full Warranty.
Is this needed when there is a long term O&M contract in place?
This is a discussion that may occur at times with the OEM’s during the TSA and long term O&M negotiations. When the OEM provides a full wrap contract, at a fixed cost, labour, parts and extra’s with an availability guarantee then what else is needed as the OEM is responsible?
To some extent the argument is valid if the only concern is related to preventing outright failures. Managing a Wind Park with long term O&M contracts may provide a higher level of comfort to lenders or even some owners. However, it also means that understanding and optimising the performance of the asset is left with the OEM. There is no guarantee that this will be a priority for the OEM. Inspections might either never take place or they might come at a higher cost. You also risk not addressing minor failures or systemic faults that are reducing the performance of the asset.
In any long term agreement, setting key performance measures at defined periods to assess the performance of the assets and the teams managing the asset is a fundamental requirement of the owner.
For example the Turbine oil heating system can be malfunctioning and as a result the cooling system will be operating more to compensate for higher oil temperature. While this may not cause short term damage to the oil, the constant running of the cooling system will mean higher parasitic load.
So if the only determining factor to perform an inspection is if there is knowledge of failures, then not only has the money paid for the warranty been wasted, but there may also be even more lost over the lifetime of the project in underperformance.
Long term agreements have a place and purpose depending on the type and experience of the owner. Assessing the performance of the Turbines and the way in which the asset is being managed by the O&M Company does come at a price.
It may be difficult to find a way to justify the cost to perform EOW inspections under a long term O&M agreement. Not understanding or even attempting to get the truth on the assets long term performance not only reduces the revenue made by the Turbine but may also be reducing the life of the Turbine.
As the production of the Wind Turbines is dependent on a variable resource, analysing, optimising and ensuring the Turbine is being managed, maintained and operated is highly recommended.
Building a scope for the inspections
This whole process would normally be designed to encompass the data from handover punch lists, commissioning sheet, the operating data and the equipment performance and then determining what level of detail and inspections are required.
For the sake of determining how to manage the EOW inspection on a Wind Park, one method would be to sub-divide the project into separate disciplines, very similar to the manner in which a project is constructed. Wind Turbines, Electrical and Civil works. From here a list / tree of sub-systems under the core discipline are created. The sub-systems are then linked to discrete tasks that an inspection company would perform. It is always advisable to link the inspection routine to the O&M manuals as provided during the handover of the projects. Using judgement and knowledge of the Type and model of Turbine, mixed with information from other owners, an optimal inspection regime can be built.
Another method would be to just allow a 3rd party company to price for the task and then check if the inspection routine meets a minimum standard.
Deliverables by EOW team
- Risk Assessments and Method statements for all work.
- Equipment Certifications
- Daily updates with owners representative noting status of inspection & High level issues
- Draft reports within 20days of inspections
- Final report within 10 days after draft report and spreadsheet list of items
Classifications of findings
A standard severity classification system is used, with visual indicators. To obtain the best value from the inspection company or team moving towards more severity scale of 5 or more classifications will allow the owner not to sort and move the OEM towards resolving.
Level |
Severity |
Criteria |
Action |
1 |
Acceptable |
Meets the standard, or no findings |
None |
2 |
Low |
Does not meet the standard and has no impact on production or safety if left unattended to within the next 6 months |
Can be completed at the next service or within 6 months ( note if the number of low items exceeds % of all finding then consider grouping all items as medium ) |
3 |
Medium |
Does not meet the standard and has no impact on production or safety or has an economic value of greater than €10K and can be left unattended for up to 1 month |
Can be repaired within 1 month |
4 |
High |
Impact on performance and production but no safety issues |
Repair within 1 week/td> |
5 |
Urgent |
Impacts both safety and performance |
Stop turbine |
Options for performing EOW
- Self-perfoming
- 3rd party contracted
- Self-performing mixed with 3rd party specialist
Selection criteria for a 3rd party inspection company
Balancing cost over quality is always a challenge and getting that optimal inspection regime is key. Below you can review some desirable quality criteria:
- Experience
- Turbine model or type
- Number of projects
- Skills
- Wind turbine Maintenance Training
- Electrical safety skills
- GWO or similar recognized
- Working at heights certified training
- Borescope training
- First aid
- Mobile Elevated W orking Platform trained ( if using to inspect blades )
- Rope access training
- Certified to use Turbine Lift
- Equipment & tools
- Borescope tools
- Climbing harness
- PPE
- Cameras
- Reports (examples)
- Blade inspections
- Tower inspections
- Borescope inspections
- Transformer inspections
- Referrals
- Safety statistics
Also review the most important cost criteria, when selecting a 3rd party for your EOW inspection:
- Cost per WTG
- Mobilisation and Demobilisation cost
- Extra equipment costs. Sometime this is a hidden cost depending on the scope of work as required by the owner, for example performing a up close blade inspection an owners H&S department may have a position that a MEWP or crane is the safest option. This cost would be an extra cost.
- Insurances – as a minimum must meet some insurance requirements ( All Risk, Employer liability ), ensure that a check the limit of Professional Indemnity is enough in the case that sub optimal advice is given.
- Cost for extra consultations if needed with OEM’s or legal court case – best agreed up front.
Finding issues
In building a comprehensive EOW inspection, it is recommended that collating a number of data sources, such as punch lists and service reports. Monthly reports by the OEM’s, and SCADA data then guides and provides signposts to discovering known and unknown issues. This work is usually performed prior to the inspection arriving on the site. The end goal is to sift through the data and then ensure that each turbine has a specific list of failures or checks over and above the generic checks.
So how is this done?
- Monthly reports, service reports and punch lists are collated and sorted to list and check the close out of issues. These are an excellent source of data to creating a list showing what are the main issues, later while in the Turbine an inspector checks or verifies are still occurring or have in fact been resolved within the Turbines.
- SCADA data is sorted on a monthly basis to create a Pareto Analysis or the top 10 alarms are listed, and further analysis is done to understand the reason behind these alarms to identify if there is any underlying cause for the alarm.
Managing the claim process with the OEMs
In many wind companies there is a common belief that a EOW claim is best handled informally with the OEM, the reasoning being that if the formal route is followed, resolution of the issue will take time. Various stories are given such as “a senior manager must now approve”, “the organisation is slow to refund the expense” or that “the service department can resolve issues faster”.
It must always be remembered that between the owner and OEM is a legal agreement where, for a consideration (payment), certain services or goods are provided. Not placing a formal claim does certainly diminish (or render void) owners’ rights to make a lawful claim if there is a major failure after the warranty period has expired. If no formal claim is made it is given that any failure after the expiry of the defects notification period, i.e. the warranty, is not covered.
So what is the suggested process?
- Complete the inspections at least 3 months prior to the end of the warranty period
- Sort the list of findings and characterise ( e.g. high, medium or low )
- Estimate the cost for each repair ( be sure to capture unseen costs such as outages or extra costs such cranes ) – This is for your own information
- Schedule a meeting with the OEM and share the list ( its recommended that the formal reports are not provided at this stage, if the OEM is fulfilling its obligations under the TSA & O&M agreements none of these items should be a “surprise”, allow the OEM to refute the claim before showing the reports )
- At the meeting work through each item and capture any agreement with close out dates to close out items. Formalise the meeting agreement by sending the minutes of the meeting. Request a formal notification of recognition that agreed items will be closed out.
- Items not agreed, here as the owners take any information that may have been provided and share with the inspection company and after discussion it may be that the issue is in fact closed or it may be that the issue is still a concern and now proceed to a formal claim.
- Formal claim and append the original list of Items. On the list note the rejected/open items, closed items and Accepted Items with agreed timelines for resolution.
- Agree to meet to work out the close out items, the OEM should be requested to bring technical people to the meeting.
In legal agreements there is normally a clause set out as a notifications clause, this lists the manner and the name of the contact person to whom a formal claim is made. If the agreement stipulates Fax then always FAX and also send by Email. Not following a formal process in agreements can impact on the success of a later legal claim under the Dispute resolution processes.
Credit
Kelly Dallas, moderator at O2O Wind International
Kelly is our senior moderator on the o2o Wind International forum, with extensive experience from all phases of wind turbine generator asset management.
If you wish to connect your O&M team with their peers at O2O WIND please arrange for an introduction. After I have understood that your company fullfills the conditions set by our members to be a part of their collaboration, I will first present the business logic behind O2O WIND and how it came into making. Thereafter we will login at the actual plattform so that you can see the actual collaboration going on with your own eyes.
Any questions or considerations do not hesitate to contact me.
Kind Regards
Mårten Nilsson, Head of Collaboration at O2O WIND International
+46-760-21 71 77 or marten@o2owind.com